Space
The Status Quo
vs. Carbice
- More data
- More computing
- More transmission
- Smaller envelope
- Conventional TIMs
- Overheating
- More heat
- More parts
- Conventional TIMs
- Larger radiators & more heat pipes
- Larger radiators
- More heat pipes
- More bolts
- More gap fillers
- Heavier spacecraft
- Dynamic interface
- Potted inserts pullout
- Conventional TIMs
- Shorter lifespan
- Pervasive TIMs
- Waste from rework
- Waster from redesign
- Hard to recycle
- More emission & waste
- Messy liquid TIMs
- Long curing time
- Scraping to rework
- Hard to simulate
- Trial-and-error design
- Painful experience
Space Pad® cools Large Bolted Interfaces better, with confidence
Spacecraft face the harshest environments for thermal management, with intense radiation, large temperature variation, and limited ways for heat to move.
Machining errors and bowing issues make large bolted interfaces non-uniform.
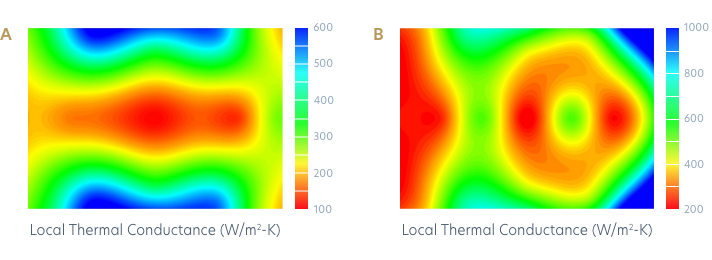
Takeaway:
In reality, large bolted interfaces have thermal gradients even with liquid TIMs.
Digital transformation of satellite design with Carbice
Carbice SIM predicts Space Pad performance with >90% accuracy.
For conventional TIMs, simulated performances could mismatch TVAC results by >50%. On the contrary, performance of Space Pad can be accurately simulated by our modeling tool - Carbice SIM.
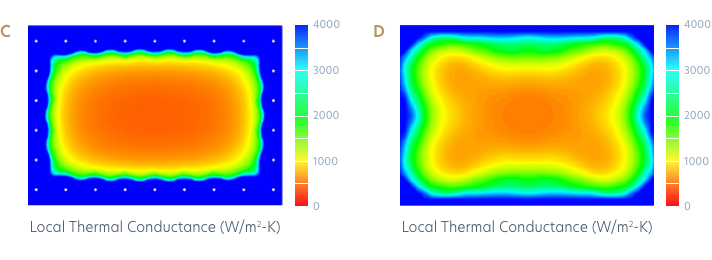
Takeaways:
- Space Pad outperforms liquid TIMs and exceeds customer thermal requirement for large bolted interfaces.
- TVAC result of Space Pad matches Carbice SIM result within ±10%.
Game changing customization
Structured Space Pad™
We can map and model your entire interface to create Structured Space Pad customized for your large bolted interface. For instance, when you have a hotspot, you can force better contact with Structured Space Pad.
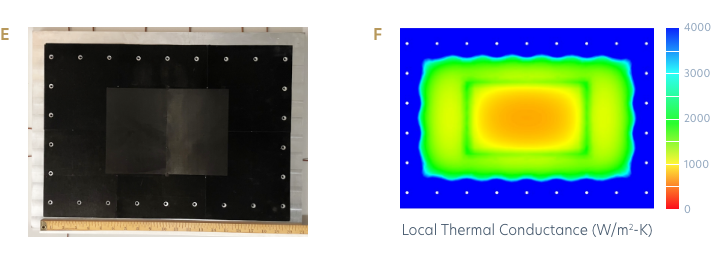
Takeaways:
- Carbice SIM matches TVAC result of Structured Space Pad within ±10%.
- Structured Space Pad provides optimal solution customized for your large area interface, minimizing hotspot.
Proven and trusted pain-free experience for space
No more painting, week-long curing, and painful scraping with liquid TIMs. No more compression set, bolt torque loss, and potted insert pullouts with conventional dry pads.
Carbice Space Pad is a clean, pain-free dry TIM trusted by primes in the space industry:
- TRL9 qualified
- Peel-n-stick to apply and rework
- Designed to outlast your mission
- Orbiting earth in satellites
- Delivered from AS9100D certified manufacturing
Additional benefits reported by customers:
- Same pad can be used both for ground testing and in flight
- Reduced spacecraft weight, saved space and saved total cost of ownership
- End-of-life performance even exceeds beginning-of-life performance
- Efficient and cost-effective to test new designs over accurate digital iterations
[1] Rafael Lopes Costa, Valeri Vlassov. "Spacecraft Electronic Boxes Thermal Contact Resistance Experimental Study." Spacecraft Thermal Control Workshop, El Segundo, California, March 28-30, 2017
Experience digital transformation of satellite design with Carbice
Step 1:
Share your assembly design with our team.
We will interface and work within your model securely.
Step 2:
Using our Carbice SIM software, we capture and predict performance accurately.
We help you lower the cost of generating drawings, and help you reach optimal thermal performance and power density with unprecedented design speed.
Small changes with big results: As an example, by adding center bolts on a particular prototype:
- Increases conductance to 1.7X
- Reduces peak delta T by 75%
- Reduces weight by 40% if kept at the same conductance
These kinds of optimizations allows engineers to design the next satellite with only half the surface area needed for cooling.
Step 3:
We prepare a small batch of samples.
We produce small batch samples with cutouts and boltholes matching your design to achieve the optimal thermal performance shown in our simulations. These samples are ready for testing.
Step 4:
When you receive the samples, follow the simple instructions to add Space Pad to your assembly.
Carbice Space Pad is as easy as peel and stick. No more painting, drying or scraping as with liquid TIMs.
Step 5:
Test your assembly. You’ll note the TVAC results agree with the Carbice SIM results within 10%.
The same Carbice Space Pad can be used in ground test and in flight with no loss in performance, no more re-painting, re-drying or re-scraping.
Step 6:
Easily integrate Space Pad into your manufacturing operations and supply chain.
Carbice Space Pad is easily added to any existing or innovative assembly process, and allows you to revolutionize your ability to lower inventory cost and lead time, while enabling you to:
- Save time,
- Streamline labor,
- Reduce weight,
- Shrink size,
- Lower the costs of annual spacecraft build
Carbice Space Pad is guaranteed to provide consistent performance and outlive your mission.