Solutions,
not just materials.
Unlike conventional TIM suppliers, we don’t kick-off a customer engagement sending data sheets and material samples. Our method arrives at better solutions faster—and with lower total cost of ownership.
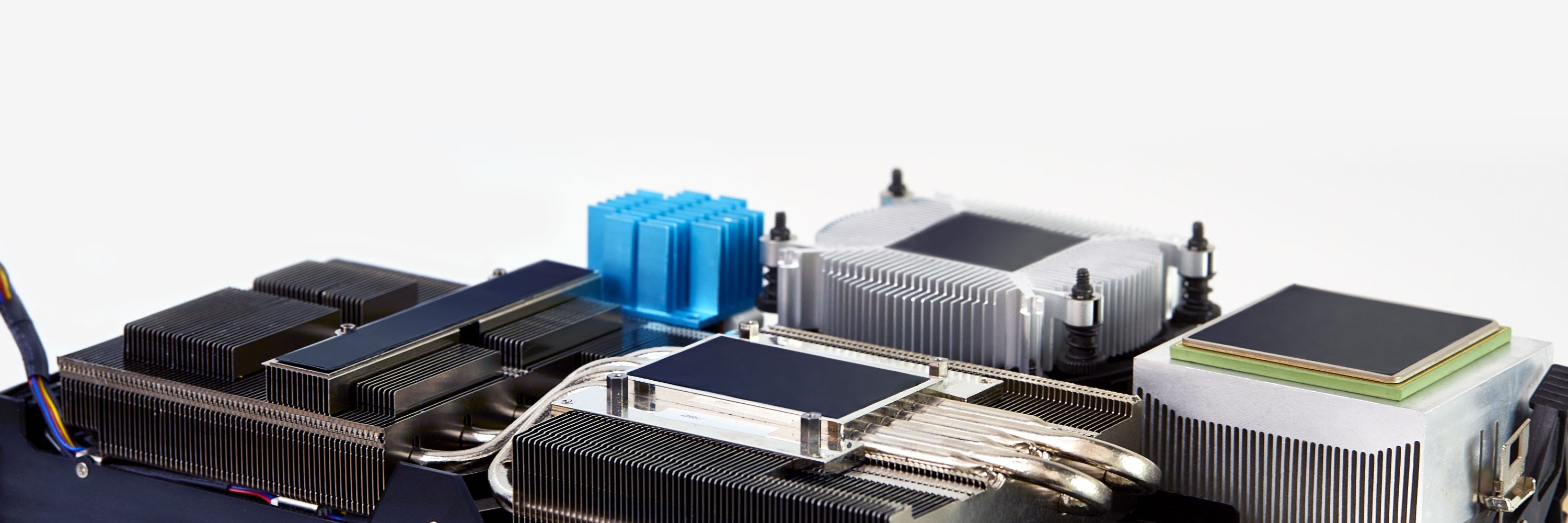
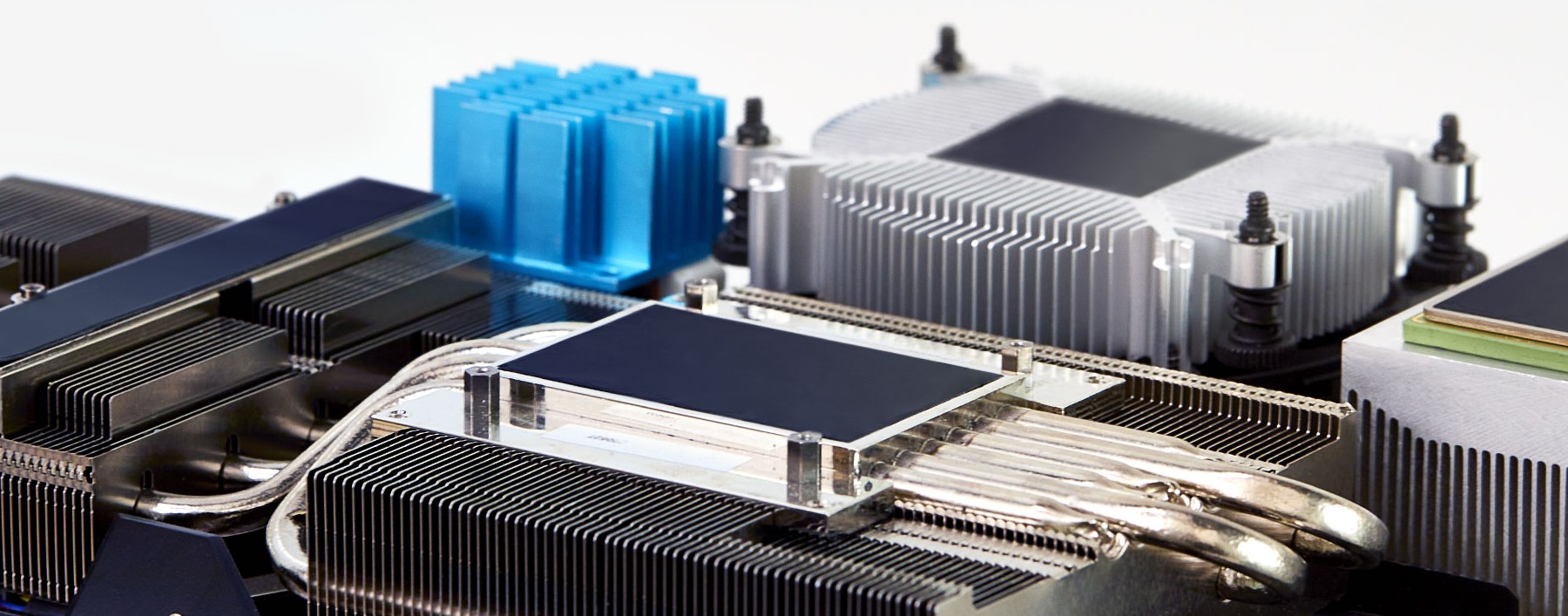
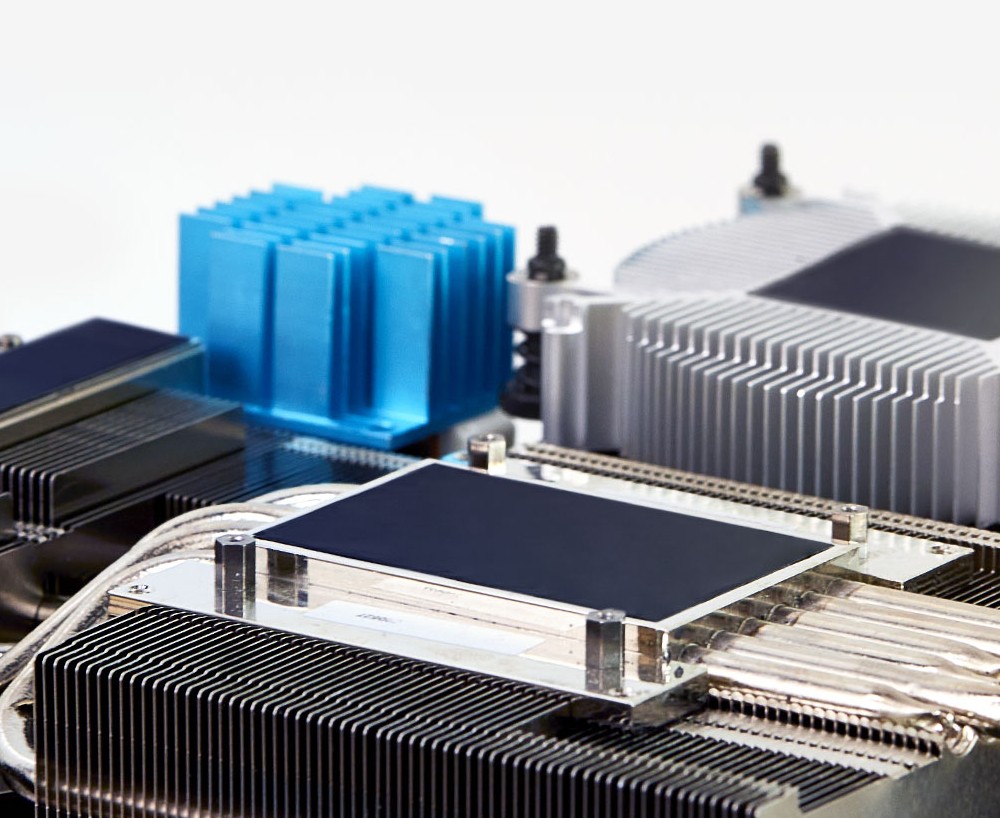
Learn more about our suite of revolutionary thermal interface materials along with their customization options.
The Carbice Method
1-2 Weeks
We ask questions about your application, understand its thermal management design, and determine what’s needed.
1-3 Weeks
We look at our product portfolio and customization options and narrow down our recommendations, running sophisticated Carbice® SIM models.
8 Weeks
First we manufacture a small batch of Carbice Pads. Then, using our lab or yours, we test that material. That material usually meets customer requirements thanks to our proven modeling.
4 Weeks
We manufacture Carbice Pads according to your specs, cut the sheets based on your designs, and deliver easy-to-mount material.