Space Pad® 
Tell us what challenges you’re facing, and we’ll work with you to find the best solution.
Space Pad® cools Large Bolted Interfaces better, with confidence
Spacecraft face the harshest environments for thermal management, with intense radiation, large temperature variation, and limited ways for heat to move.
Machining errors and bowing issues make large bolted interfaces non-uniform.
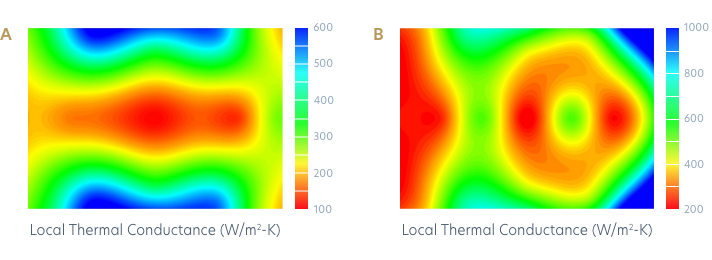
Takeaway:
In reality, large bolted interfaces have thermal gradients even with liquid TIMs.
Digital transformation of satellite design with Carbice
Carbice SIM predicts Space Pad performance with >90% accuracy.
For conventional TIMs, simulated performances could mismatch TVAC results by >50%. On the contrary, performance of Space Pad can be accurately simulated by our modeling tool - Carbice SIM.
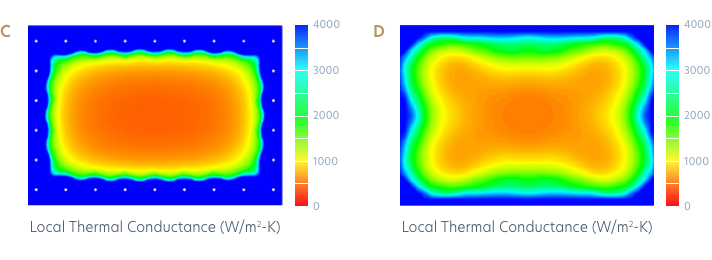
Takeaways:
- Space Pad outperforms liquid TIMs and exceeds customer thermal requirement for large bolted interfaces.
- TVAC result of Space Pad matches Carbice SIM result within ±10%.
Game changing customization
Structured Space Pad™
We can map and model your entire interface to create Structured Space Pad customized for your large bolted interface. For instance, when you have a hotspot, you can force better contact with Structured Space Pad.
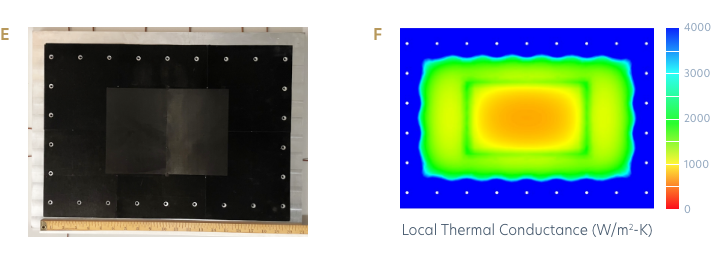
Takeaways:
- Carbice SIM matches TVAC result of Structured Space Pad within ±10%.
- Structured Space Pad provides optimal solution customized for your large area interface, minimizing hotspot.
Proven and trusted pain-free experience for space
No more painting, week-long curing, and painful scraping with liquid TIMs. No more compression set, bolt torque loss, and potted insert pullouts with conventional dry pads.
Carbice Space Pad is a clean, pain-free dry TIM trusted by primes in the space industry:
- TRL9 qualified
- Peel-n-stick to apply and rework
- Designed to outlast your mission
- Orbiting earth in satellites
- Delivered from AS9100D certified manufacturing
Additional benefits reported by customers:
- Same pad can be used both for ground testing and in flight
- Reduced spacecraft weight, saved space and saved total cost of ownership
- End-of-life performance even exceeds beginning-of-life performance
- Efficient and cost-effective to test new designs over accurate digital iterations
[1] Rafael Lopes Costa, Valeri Vlassov. "Spacecraft Electronic Boxes Thermal Contact Resistance Experimental Study." Spacecraft Thermal Control Workshop, El Segundo, California, March 28-30, 2017
Space Pad® keeps Traveling-Wave Tube Amplifier cool
Challenge of heat management of high power components on spacecraft
TWTAs are exposed to extreme temperatures that influence the strength and stability of their magnetic field and can adversely affect their RF signal output. However:
- Conventional TIMs are a pain to apply and difficult to rework
- Large disagreement between simulated results using conventional TIMs and tested results from thermal vacuum chamber test (TVAC)
- The thermal interface of conventional TIMs degrades over time, compromising performance
Meet Carbice Space Pad
SP125x-1S
Space Pad is the standard for space applications:
- TRL9 qualified TIM, orbiting earth now in satellites since 2018
- Reliable performance accurately predicted by our simulation tool Carbice SIM
- Easy to apply and painless to rework compared to grease and LSR
- Same pad can be used both for ground testing and in flight
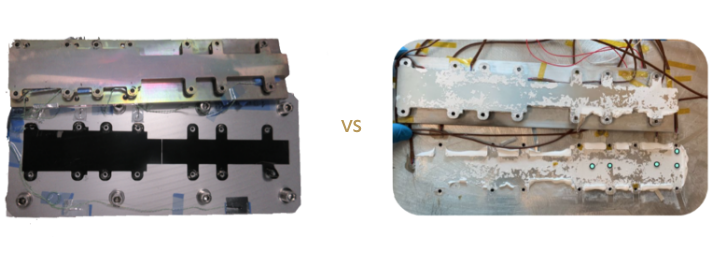
Customized Carbice Space Pad SP125x-1S for this TWTA application:
- Low-outgassing solid pad
- One-sided tack
Results
SP125x-1S
- Performance in ASTM D5470 reference bar: 17,000 W/m²-K
- Performance in application: 11,000 W/m²-K
- Maintained stable performance before and after thermal cycling
- Manufacturing advantage validated by engineers and technician
Values for customers
Space Pad
Major primes in space industry have chosen Space Pad over other TIMs for their spacecraft to:
- Get design-phase support with accurate simulations using Carbice SIM
- Get industry leading thermal conductance
- Establish confidence in thermal performance stability throughout mission
- Reduce payload weight, save space and save cost
- Take advantage of painless user experience validated by engineers and technicians