Power Modules
The Status Quo
vs. Carbice
- New chip technology
- More power density
- Faster switching speed
- Smaller footprint
- Liquid TIMs
- Overheating
- Dynamic interface
- Harsher environment
- Liquid TIMs degrade
- Shorter lifespan
- Liquid TIM
- Excess material
- Higher tool investment
- Shorter lifespan
- Higher cost
- Pervasive TIMs
- Excess material waste
- Shorter device lifespan
- Hard to recycle
- More emission & waste
- Liquid TIMs
- Higher temp ICs
- Dynamic interface
- Require baseplate
- Larger cooling system
- Bulky device & performance derate
- Liquid TIMs
- Messy process
- Degrades over time
- Require onsite stencil process
- Painful experience
Carbice® Pad provides better long-term cooling than other TIMs
Electronic devices experience an increasing number of heat management challenges:
- Smaller and more powerful electronics lead to thermal expansion mismatch
- Thermal expansion mismatch causes electronic malfunction and shortens lifespan
- Conventional TIMs fail to dissipate heat over time due to dry-out, pump-out, and formation of air voids
- Electronics de-rate, degrade, and are disposed as e-waste after a short time
High-Performance Grease C-SAM Analysis
Grease was applied only at the center of the interface (within the dotted circle).
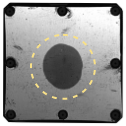
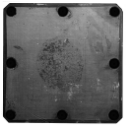
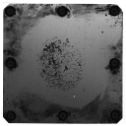
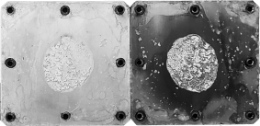
Takeaway:
After only ~50 cycles, the grease has completely dried out.
High-Performance PCM C-SAM Analysis
PCM was applied over the entire interface.
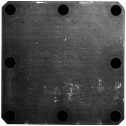
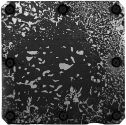
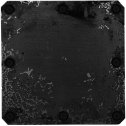
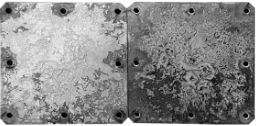
Takeaway:
Air voids migrate around interface with PCM.
Carbice Pad C-SAM Analysis
Carbice Pad IP150 was applied over the entire interface.
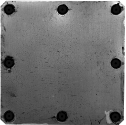
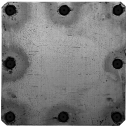
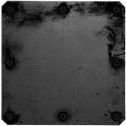
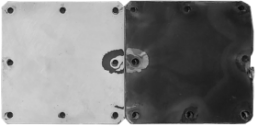
Takeaway:
Carbice Pad cause no interface degradation throughout the 2000 test cycles.
Coupon thermal resistance change due to thermal cycling
Thermal cycling performed from -55 °C to 110 °C for 2000 cycles, according to modified JEDEC standard JESD22-A104F condition L. Thermal conductance measured using ASTM D5470 standard testing method.
Thermal interface quality degrades with increasing cycles for conventional TIMs:
- After 2000 cycles the thermal resistance of grease is 2.6 times that of Carbice Pad
- After 2000 cycles the thermal resistance of PCM is 1.4 times that of Carbice Pad
Using Carbice Pad, customers are able to:
- Remove heat effectively and reliably over time
- Expect less de-rating of electronics over time
- Build higher performance electronics that last longer
- Generate less e-waste and be more sustainable
Carbice® Pad enables better cooling for GPU
The challenge of GPU heat management
GPUs are incorporated by data centers to handle increasingly intensive workloads:
- They are affected by large thermal variances during operation
- Heat buildup reduces GPU’s performance, stability and lifespan
- Reliability of data centers will be compromised
Meet Carbice Pad
Carbice Pad provides high thermal conductivity of a solid TIM and low thermal resistance of a liquid TIM, with reliable long-term performances and high volume manufacturability. For this study, we used IP90 with 2-sided assembly tack.
Carbice Pad demonstrated immediate better cooling and long-term gains to GPU performance compared to POR Grease:
- 2℃ cooler upon initial installation
- > 6℃ cooler after extended use
Over time, grease pumps-out and develops dry-cracks, causing its thermal resistance to double after extended use. On the contrary, Carbice Pad wets the interface even better with time and cycling.
Takeaway:
Carbice Pad provides better lifetime cooling performance than grease.
Using Carbice Pad, customers are able to:
- Lower GPU temperature
- Boost GPU performance
- Extend GPU lifespan
- Increase data center reliability